Sostituzione dei bruciatori a condotto nelle centrali a ciclo combinato
CATEGORIE:
Sostituzione dei bruciatori a condotto nelle centrali a ciclo combinato
Molte centrali elettriche a ciclo combinato (CCPP) e impianti di cogenerazione o di produzione combinata di calore ed energia (CHP) utilizzano sistemi di combustione supplementare, o bruciatori a condotto, all'interno delle caldaie del generatore di vapore a recupero di calore (HRSG). I bruciatori a condotto possono essere attivati su richiesta per aumentare in modo rapido ed efficiente la produzione di vapore dell'HRSG al generatore di turbine a vapore per aggiungere megawatt nelle centrali di cogenerazione e cogenerazione, dove la produzione di megawatt può essere su richiesta o pre-pianificata dal dispacciamento applicabile del produttore per sostenere la domanda di elettricità. I bruciatori a condotto possono anche aumentare la produzione di vapore per l'uso da parte dei clienti, con conseguente aumento delle vendite per il produttore di cogenerazione.
In tutto il mercato nazionale, molti bruciatori a condotto sono stati installati in CCPP e cogen/CHP greenfield costruiti tra il 1995 e il 2005. Le installazioni di bruciatori a condotto sono rallentate nelle CCPP e nei cogen/CHP greenfield tra il 2005 e il 2015. Dal 2015, la costruzione di nuovi impianti CCPP e cogen/CHP si è quasi arrestata a causa dell'economia e delle recenti pressioni da parte delle agenzie governative per la ricerca e l'investimento in tecnologie a combustibile verde. Di conseguenza, l'infrastruttura delle centrali elettriche nel mercato nazionale sta invecchiando e necessita di attenzione.
Purtroppo, a causa dell'invecchiamento dell'infrastruttura delle apparecchiature esistenti, molti sistemi di bruciatori a condotto in uso oggi hanno raggiunto o si stanno rapidamente avvicinando al ciclo di vita previsto e presentano una serie di problemi per il produttore, come ad esempio:
- Aumento dei costi di manutenzione per la riparazione continua delle apparecchiature
- Aumento dei costi operativi con emissioni più elevate o impingement di fiamma sull'HRSG
- Guasto parziale dei bruciatori, con problemi di spegnimento e affidabilità.
- Guasto completo dei bruciatori, con problemi semplici come bruciatori non funzionanti e complessi come il crollo dei bruciatori sul pavimento dell'HRSG.
- Continuo decadimento delle apparecchiature obsolete a tassi esponenziali nel tempo
Ispezioni frequenti e documentate e il monitoraggio dell'invecchiamento delle apparecchiature sono fondamentali per comprendere le condizioni attuali dei bruciatori di condotto di un impianto e per sapere quando è necessario prevedere un budget per i costi di capitale per le riparazioni o la sostituzione. Le ispezioni possono essere eseguite mentre l'apparecchiatura è in funzione, ma è preferibile eseguirle durante le interruzioni, in genere in primavera e in autunno, e dovrebbero essere eseguite da un'azienda di combustione affidabile. Queste ispezioni possono identificare i problemi che possono avere un impatto sull'apparecchiatura esistente, diagnosticare i motivi dei guasti già avvenuti e determinare se la sostituzione è più economica della manutenzione continua. Le ispezioni possono essere completate in un solo giorno, se coordinate in modo appropriato per non ritardare il riavvio dell'impianto.
La sostituzione dei sistemi di bruciatori a condotto è spesso più semplice di quanto la maggior parte dei produttori si renda conto. Questo può essere l'approccio migliore per preservare il ciclo di vita delle capacità di produzione di energia, perché la sostituzione arresta il processo di invecchiamento e ripristina l'orologio per il produttore, eliminando una delle tante preoccupazioni del team di gestione. Questo caso di studio di una sostituzione chiavi in mano di un sistema di bruciatori a condotto (Figura 1) eseguita da Zeeco aiuta i proprietari degli impianti a comprendere il percorso dalla diagnosi all'avviamento e dimostra i vantaggi dell'eliminazione delle apparecchiature obsolete dall'infrastruttura di una centrale elettrica.
La situazione
Nel 2022, un'importante azienda di produzione di energia elettrica nel sud-est degli Stati Uniti ha contattato Zeeco con preoccupazioni relative al sistema di bruciatori a condotto esistente. Zeeco ha eseguito un'ispezione di guasto e ha registrato i risultati, tra cui:
- Stabilizzatori di fiamma mal deformati
- Guasto della fiamma pilota per la fiamma principale del combustibile dell'elemento bruciatore
- Scarso riconoscimento dello scanner a fiamma
- Impingement della fiamma sulla sezione tubiera dell'HRSG a valle
Gli stabilizzatori di fiamma deformati e distorti possono derivare dall'incapacità di controllare la forma della fiamma a causa di un flusso insufficiente di gas di scarico della turbina (TEG). Ciò è generalmente causato da vecchi progetti, sempre inadeguati ma sconosciuti fino all'introduzione di nuove tecnologie. Il semplice processo di invecchiamento di un'apparecchiatura di combustione sottoposta ad anni di accensione e spegnimento consuma anche i portafiamma e i corpi di fumo. In questo caso, entrambi hanno contribuito al decadimento dell'apparecchiatura.
L'incapacità del pilota di accendere le fiamme del combustibile principale può derivare dal cedimento degli elementi del bruciatore. Altre cause di questo guasto sono semplicemente la distruzione dei dispositivi di scintillazione che risiedono all'interno dell'ambiente del forno HRSG giorno dopo giorno a temperature estreme. Il circuito elettrico generale dei sistemi di accensione ad alta energia è facilmente disturbato dal vapore acqueo proveniente dal TEG e dai sistemi di condotti aperti, che spesso possono essere impregnati di acqua piovana. In questo caso, il cedimento dell'elemento del bruciatore è stato la causa principale della mancata accensione del combustibile principale da parte del pilota. Le punte delle scintille non si trovavano più nel percorso del combustibile principale e non avevano alcuna possibilità di accendersi.
Anche lo scarso riconoscimento della fiamma del combustibile principale da parte dello scanner di fiamma può essere attribuito a diversi problemi:
- Elementi del bruciatore cedevoli.
- Sporco, detriti o vapore acqueo ricoprono la lente dello scanner a fiamma.
- Movimento involontario del sistema di montaggio dello scanner di fiamma dovuto alle normali e forti vibrazioni dell'HRSG.
- I modelli di scanner più vecchi utilizzano algoritmi di riconoscimento della fiamma obsoleti che non sono in grado di distinguere correttamente tra fiamma e assenza di fiamma.
I componenti elettronici non durano in eterno e possono facilmente causare un cattivo riconoscimento della fiamma.
In questo caso, gli scanner erano di vecchia tecnologia e si erano usurati in varie fasi su più livelli del bruciatore.
L'impingement della fiamma sulla sezione del tubo HRSG a valle è la principale causa di distruzione delle caldaie HRSG, che costa milioni di euro per riparare i lunghi tubi in lega della caldaia. Le fiamme lunghe e pigre creano l'impingement della fiamma quando il sistema del bruciatore introduce il combustibile grezzo nel forno HRSG (sotto il pieno controllo del sistema di gestione del bruciatore [BMS]) e viene acceso dall'accenditore pilota. Una volta che la fiamma del combustibile principale è accesa e riconosciuta dallo scanner di fiamma, il sistema di controllo distribuito (DCS) dell'HRSG consente di aumentare il combustibile per soddisfare la domanda di vapore in uscita.
Tuttavia, quando le punte dei bruciatori si erodono sotto la pressione del combustibile nel corso del tempo, o gli stabilizzatori di fiamma si deformano a causa del ricircolo del flusso di TEG e della fiamma del bruciatore, o quando gli elementi del bruciatore si abbassano (Figura 2), il combustibile può fluire ulteriormente a valle della punta del bruciatore prima che avvenga la combustione effettiva o completa. Questi fattori possono consentire alle fiamme di allungarsi fino a impattare sui tubi. Nel corso del tempo, l'impingement distruggerà i tubi. Questo problema deve essere corretto, altrimenti il guasto futuro è imminente. In questo caso, le fiamme più lunghe causate dall'erosione delle punte dei bruciatori hanno contribuito all'impingement della fiamma.
La sfida
Questo progetto comprendeva sfide comuni e specifiche per ogni situazione. In particolare, l'interruzione pre-pianificata era prevista per 18 giorni in primavera ed era classificata come un'interruzione non importante, il che significa che non erano previste modifiche alla turbina a combustione o alla turbina a vapore durante l'interruzione. In molti siti le interruzioni sono comunemente pianificate con largo anticipo, il che rende molto importante la comprensione delle condizioni esistenti delle apparecchiature dei bruciatori a condotto, in modo da poterne completare la sostituzione senza interrompere o alterare i programmi di interruzione pre-pianificati.
Il cliente ha inoltre spiegato che questo impianto era critico per la rete, in quanto la richiesta di produzione di vapore e di megawatt era della massima importanza a causa dell'enorme base di clienti. Non è stato possibile evitare la tempistica dell'interruzione e l'unità doveva essere operativa l'ultimo giorno dell'interruzione. La prossima interruzione programmata per questo sito non era prevista prima di diversi anni, il che aggiungeva un'altra importante considerazione all'apparecchiatura e all'installazione. È stata necessaria un'ampia pianificazione chiavi in mano per affrontare questa sfida temporale e una comunicazione costante con la struttura.
In genere, la progettazione e l'installazione devono rientrare nel valore di costo del budget di capitale pre-approvato per l'interruzione. In questo caso, il cliente aveva approvato un budget di capitale circa due anni prima dell'acquisto dei nuovi bruciatori. Tuttavia, l'inflazione dell'economia e la pandemia di reincidenza hanno fatto sì che i prezzi dei materiali costituissero un problema imprevisto.
La tempistica della richiesta di offerta rispetto alle date di interruzione dell'installazione è stata la chiave del successo. La progettazione, la fabbricazione, la consegna e l'installazione richiedono ciascuna un certo numero di settimane rispetto al programma generale per essere eseguite con successo. Pertanto, era fondamentale ordinare l'apparecchiatura con largo anticipo rispetto al programma di interruzione previsto. Anche in questo caso, la comprensione delle condizioni esistenti delle apparecchiature del bruciatore a condotto ha permesso al proprietario dell'impianto di pianificare correttamente la sostituzione.
Processo del progetto
La progettazione del retrofit è stata completata da un team di grande esperienza che ha eseguito con successo numerosi progetti di sostituzione chiavi in mano di bruciatori da condotto, oltre a progettare e fabbricare bruciatori da condotto greenfield per un ampio elenco di produttori di apparecchiature originali in tutto il mondo. Mantenere un team di ingegneri e manager sul progetto rafforza le relazioni con il team del cliente ed elimina le lacune informative nell'ambito del progetto.
Gli acquisti di materiale sono stati completati da personale ampiamente addestrato a trovare i prezzi e le consegne migliori. Zeeco utilizza un ampio elenco di produttori approvati, monitorati dal suo programma ISO (International Organization for Standardization), che conferisce un enorme potere d'acquisto agli acquirenti coinvolti ed elimina la necessità di preoccuparsi di fornitori nuovi o non testati.
La fabbricazione dell'apparecchiatura in uno dei sette stabilimenti di produzione globali di Zeecoè stata fortemente monitorata dal team di assicurazione/controllo qualità (QA/QC) e dal team di progettazione per l'esecuzione del progetto. La consegna è stata pianificata ed eseguita da un team logistico di esperti di trasporti. Prima della fase di esecuzione del progetto, Zeeco ha creato uno schema e un piano chiavi in mano altamente specifico per tutti i lavori meccanici ed elettrici da eseguire in loco. Il piano implementato è stato seguito da squadre di costruttori esperti.
Scoperta
Quasi tutti i progetti di installazione "chiavi in mano" producono una scoperta che identifica problemi sconosciuti prima dell'inizio della demolizione delle apparecchiature esistenti. Nel caso di questo progetto, la scoperta è stata una grave corrosione interna delle pareti dell'involucro in acciaio al carbonio dell'HRSG (Figura 3). Questo tipo di scoperta è sempre più comune per le vecchie apparecchiature HRSG e per i bruciatori a condotto, in particolare quando le unità HRSG sono state originariamente installate in prossimità di ambienti a rischio o in luoghi in cui le temperature estreme possono far lavorare in modo straordinario l'involucro esposto, l'isolamento delle pareti dell'HRSG e il sistema di piastre galleggianti interne dell'HRSG.
Altri problemi comuni a questi tipi di HRSG e bruciatori a condotto sono la corrosione interna delle tubazioni del combustibile, la riduzione dello spessore delle pareti delle tubazioni in pressione e la corrosione o distruzione delle sedi delle valvole. Questi problemi si sviluppano nel tempo a causa delle fluttuazioni della temperatura del combustibile in tutta l'infrastruttura di tubazioni dell'impianto, causate da condizioni climatiche e stagionali variabili. Per questo progetto era già prevista la sostituzione delle tubazioni esterne con nuove tubazioni, raccordi e valvole esenti da corrosione.
La soluzione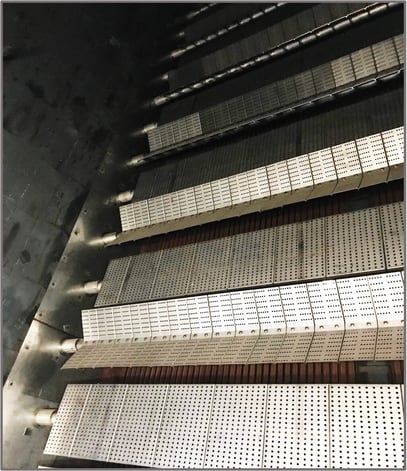
Questo progetto di sostituzione del bruciatore a condotto chiavi in mano è stato pianificato tenendo conto di questi tipi di scoperta comuni. Ogni potenziale scoperta viene discussa con il cliente prima di finalizzare l'acquisto dell'apparecchiatura e l'installazione chiavi in mano. La riduzione delle scoperte in anticipo attraverso una pianificazione dettagliata crea un programma di prestazioni che è il più accurato possibile rispetto agli scenari reali e aiuta a eliminare le sorprese.
Durante un'interruzione programmata, altri appaltatori sono spesso sul posto per eseguire lavori su altre apparecchiature, come le torri di raffreddamento o le vasche del tamburo della caldaia e le valvole di sicurezza. Il sito può diventare congestionato e i rimorchi per gli attrezzi e gli uffici per la costruzione possono ridurre le zone di stazionamento dei materiali. L'utilizzo di un'azienda di installazione affidabile e la partecipazione quotidiana alle riunioni di interruzione offrono a tutti gli appaltatori la possibilità di esprimere e condividere quotidianamente le proprie preoccupazioni e i propri piani. Il coordinamento tra gli appaltatori può evitare problemi come la competizione per l'assegnazione di una gru o di spazi per il carroponte e le distanze per l'esame radiografico non distruttivo, nonché la congestione stradale dovuta alla consegna di materiali e materiali di consumo. Un progetto ben comunicato è un progetto più sicuro, che elimina gli incidenti e potenzialmente salva la vita.
Risultati e benefici
Dopo l'avvio di questo progetto e la smobilitazione della squadra di installazione, i vantaggi per questo cliente sono stati molto chiari. Ciascuno dei seguenti punti ha soddisfatto le esigenze del cliente e ha ridato al sistema di bruciatori a condotto la vita necessaria per molti anni.
Successo chiavi in mano
La sostituzione del bruciatore a condotto è stata completata in 16 giorni invece dei 18 previsti, consentendo la riaccensione dell'unità l'ultimo giorno dell'interruzione.
Costo
In questo caso, il potere d'acquisto globale di Zeecoha permesso al team di procurarsi i materiali e di risparmiare il valore del budget di capitale originale creato con largo anticipo rispetto all'acquisto dell'apparecchiatura.
Nuova attrezzatura
Il cliente dispone ora di un nuovo sistema di bruciatori a condotto senza i problemi precedenti. Il risparmio finanziario derivante dalla riduzione dei costi di manutenzione e di funzionamento si tradurrà in un risparmio nel tempo.
Attrezzatura corretta
Il progetto e l'installazione sono stati conformi al 100% alle specifiche, il che significa che il cliente ha ricevuto tutto ciò che aveva chiesto con un solo intervento e con un solo costo.
Rilascio di calore
La nuova apparecchiatura fornisce la giusta quantità di calore rilasciato nella caldaia HRSG per una produzione di vapore ottimale.
Fabbricazione
Zeeco ha utilizzato uno dei sette stabilimenti di produzione globali interni per completare l'apparecchiatura nei tempi previsti e nel pieno rispetto dei requisiti interni e di QA/QC del cliente.
Consegna
Sapere che le attrezzature acquistate sarebbero state consegnate al sito utilizzando il sistema logistico del fornitore ha permesso di risparmiare molte ore di supervisione e preoccupazione da parte della direzione del cliente.
Installazione
Questa installazione "chiavi in mano" ha utilizzato una delle tante squadre di installazione meccanica ed elettrica che Zeeco utilizza e gestisce. Un'installazione completamente "chiavi in mano" ha inoltre risparmiato al cliente molte ore di supervisione e preoccupazione da parte del management.
Prestazioni puntuali
Il completamento del progetto è avvenuto prima del previsto e al costo preventivato, a vantaggio del produttore e garantendo che l'interruzione pianificata fosse corretta e non fosse necessaria una proroga.
Zero incidenti di sicurezza o infortuni
Alla fine di ogni giornata, tutti sono tornati a casa senza infortuni. A lungo termine, i premi assicurativi rimangono bassi, le metriche di monitoraggio della sicurezza dell'impianto rimangono ineccepibili e il record di sicurezza dell'azienda rimane inalterato.
Accesso migliorato
Le aree di accesso meno congestionate sul fronte del bruciatore consentono di migliorare la manutenzione e le operazioni, creando anche ambienti di lavoro più sicuri.
Training
La formazione del team operativo sulle nuove apparecchiature del fornitore è fondamentale per ottenere operazioni impeccabili e ridurre i viaggi inutili.
Emissioni
La tecnologia delle nuove apparecchiature riduce notevolmente le emissioni in molti casi e consente alle società operative di rimanere entro i limiti di tolleranza delle emissioni.
Protezione delle apparecchiature
Una forma della fiamma ben ancorata e una lunghezza della fiamma che si adatta bene al forno HRSG eliminano i danni alle sezioni del tubo a valle, alle pareti del liner, ai soffitti e al pavimento.
Conformità con la National Fire Protection Association (NFPA)
L'NFPA 85, l'ente che regola i bruciatori a condotto, e in particolare il capitolo 8, viene aggiornato di frequente. Se l'apparecchiatura è nuova, le misure di sicurezza sono già in vigore.
Garanzia
Le nuove apparecchiature offrono garanzie limitate ai proprietari delle strutture.